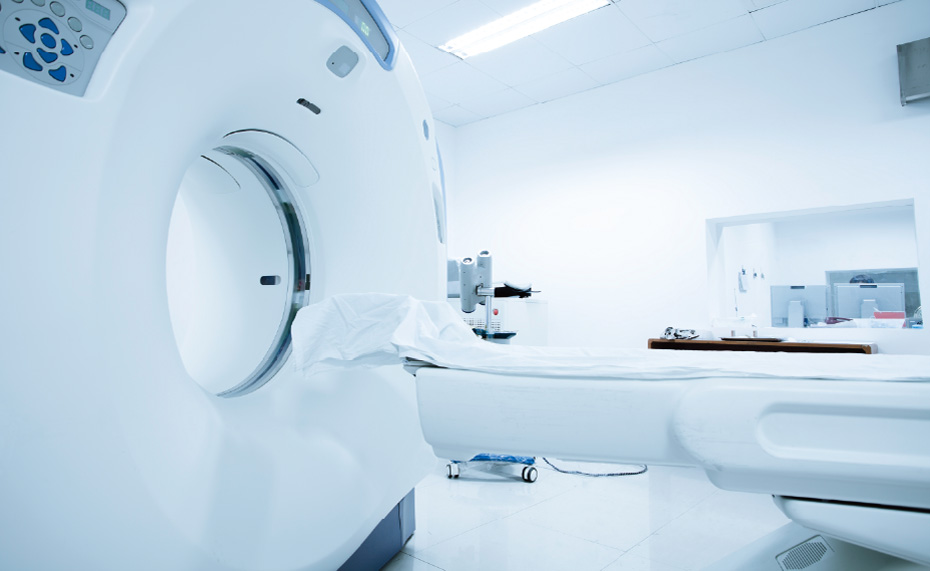
In the gradient amplifier system of MRI equipment, the output feedback from the high precision current sensor that can control the precise phase of the gradient amplifier in real time is the basis of the entire system.
The quality, sharpness and resolution of the image are directly related to the magnetic field generated by the current through the gradient coil. Therefore, the accuracy of the current sensor is one of the most critical factors that determine the current control loop.
Hangzhi multi-point zero magnetic flux gate current sensor can measure the current range of 50A-10000A, with high accuracy, small error, stable performance, and wide operating temperature range. It can be used in the power supply system of various low-energy, medium-energy and high-energy medical accelerators and gradient amplifier of MRI.
Inhoudsopgave
Understanding Current Sensors: What They Are and How They Work
Generally speaking, “current transducer”, also sometimes called “current sensor”, is a device used to measure the electric current flowing through a circuit.
It converts the current to be measured, also called primary current either AC current or DC, into signal that can be measured by the control board or instruments, which is also called secondary signal and this signal can be current, voltage or even digital signal.
There are many types of current sensors, such as Hall effect sensors, shunt resistors, and current transformers.
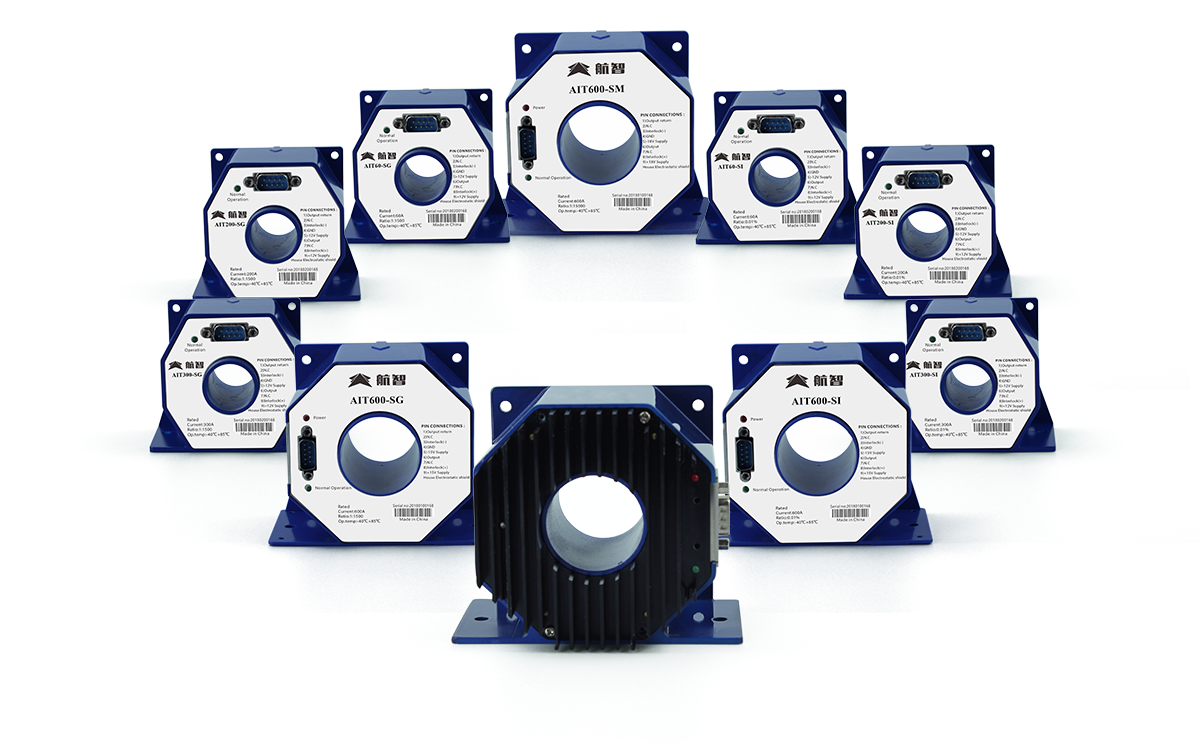
Key Considerations for Choosing a Current Sensor for Medical Equipment
When selecting a current sensor for medical equipment, several key considerations must be taken into account to ensure the sensor meets the stringent requirements of medical applications. Here are the primary factors to consider.
Accuracy and Reliability:
High accuracy is crucial in medical applications to ensure precise measurements. Digital sensors are often preferred due to their more stable and precise output compared to analog sensors.
Reliability is equally important, as medical devices must operate consistently and accurately over time. This includes rigorous testing and calibration protocols to maintain sensor performance.
Durability and Packaging:
The sensor must be able to withstand harsh medical environments, including exposure to cleaning agents and sterilization processes. Durable packaging is essential to protect the sensor from these conditions.
The sensor should also be compact and suitable for use in small spaces, which is common in medical devices.
Isolation and Safety:
Electrical isolation is often necessary to prevent electrical interference and ensure patient safety. Sensors based on Faraday’s Law of Induction, such as current transformers (CTs) and Rogowski coils, provide inherent isolation.
The choice of isolation method can affect the sensor’s cost, bandwidth, accuracy, and thermal drift, so it’s important to balance these factors based on the specific application requirements.
Biocompatibility and Safety:
For sensors that come into direct contact with patients, biocompatibility is a critical consideration. The sensor materials must be safe for use in medical environments and should not cause any adverse reactions.
Safety standards and regulations specific to medical devices must be adhered to, ensuring that the sensor meets all necessary certifications and guidelines.
Cost and Customization:
The cost of the sensor is a significant factor, especially in the design phase where companies aim to lower costs and reduce risks. There is a choice between off-the-shelf sensors, which are generally more cost-effective, and custom-made sensors, which may offer better performance but at a higher cost.
Customization options can be important for meeting specific application requirements, but they can also increase development time and costs.
Operating Environment:
The sensor must be suitable for the specific operating environment of the medical device. This includes considerations for temperature ranges, humidity, and other environmental factors that can affect sensor performance.
Integration and Compatibility:
The sensor should be easily integrable with the existing medical device systems. This includes compatibility with the device’s power supply, signal processing, and communication protocols.
By considering these factors, medical device manufacturers can select a current sensor that not only meets the technical requirements but also ensures the safety, reliability, and efficiency of the medical equipment.
Types of Current Sensors for Medical Equipment
There are many types of current sensors used in industrial applications, including:
Current transformers
These sensors use induction and the natural magnetic field to measure current. They are commonly used in industrial environments.
Shunt resistors
These resistors have a precise, low resistance and are used to measure current by measuring the voltage drop across them.
Rogowski coils
These sensors use a flexible coil wrapped around a current-carrying conductor to measure alternating current. They are used for measuring high-speed current transients, pulsed currents, or 50/60 Hz line power.
These sensors are reliable and sensitive, and can measure a few milliamperes of direct current. They are often used for battery monitors.
These sensors produce a Hall voltage when the magnetic flux density around them is above a threshold. They are well-suited for current sensing applications.
These sensors can be clamped onto existing electrical wiring to measure the current passing through.
Matching the Right Sensor to Your Medical Equipment’s Requirements
In order to ensure the accuracy of the power supply output current, the scanning power supply of the medical heavy ion accelerator (HIMM) adopts a hysteresis (closed-loop) control strategy to limit the tracking error to a very small error range, so stability and accuracy are very important.
Accuracy and reliability, durability and packaging, isolation and safety, biocompatibility and safety, operating environment, integration and compatibility, cost and customization are all factors that need to be considered.
Selecting the Right Current Sensor for Medical Equipment with Hangzhi Precision
By carefully considering these factors, you can select a current sensor that meets the stringent requirements of medical equipment, ensuring both safety and performance.
Shenzhen Hangzhi Precision Electronics Co., Ltd. is a technology-leading enterprise dedicated to the research and development, production, sales and solution customization of high-precision current sensors, voltage sensors and high-precision electrical measuring instruments.
We strive to build a well-known brand of precision current sensors and precision electrical measuring instruments in the DC field, and strive to develop into an internationally leading leader in precision electronics in the field of DC systems.