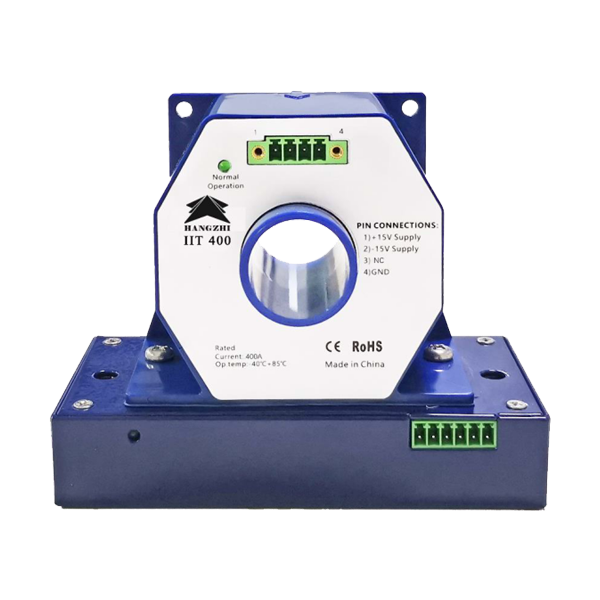
Current sensors play a key role in the rapidly evolving world of industrial automation and efficiency. These devices are essential for monitoring and controlling electrical systems, ensuring optimal performance and reducing energy consumption. Industries can significantly improve operational efficiency, cost savings, and sustainability. This article post explores how current sensors contribute to enhancing industrial efficiency.
What Does A Current Sensor Do?
UN current transducer is an electrical device that measures or converts an electrical current for monitoring or control purposes. A current transducer does the following:
Current Measurement: A current transducer’s principal duty is to properly measure the magnitude of an electrical current flowing through a conductor. This current might be either alternating current (AC) or direct current (DC).
Isolation: Electrical isolation is frequently provided by current transducers between the input current and the output signal. This isolation is critical for safety and preventing interference between various components of an electrical system.
Signal Conversion: Current transducers frequently convert measured current into a proportionate output signal, which is typically in the form of voltage or current. This conversion facilitates communication with other electronic devices such as microcontrollers, PLCs (Programmable Logic Controllers), and data acquisition systems.
Amplification: Some current transducers may amplify the current signal in order to generate a more powerful and easily measured output. In certain applications, this amplification can help enhance the precision of current measurement. For the RIT leakage current sensor peut convertir le courant avec des mini ampères en tension de 1 ou 2 V mesurable par le PLC ou les microcontrôleurs.
Les transducteurs de courant peuvent avoir une variété de types de sortie, tels qu'une sortie de tension (par exemple, un transducteur de courant de sortie 0-10 V), une sortie de courant, une sortie de fréquence ou des protocoles de communication numérique (par exemple, un transducteur de courant 4-20 mA ou Modbus). Le type de sortie utilisé est déterminé par les besoins uniques de l'application.
Accuracy and Sensitivity: Current transducers are built to deliver precise measurements within a given range. To match the intended current range, they frequently include adjustable sensitivity or gain settings.
Hangzhi current transducers include protective mechanisms to defend against overcurrent circumstances and other electrical issues.
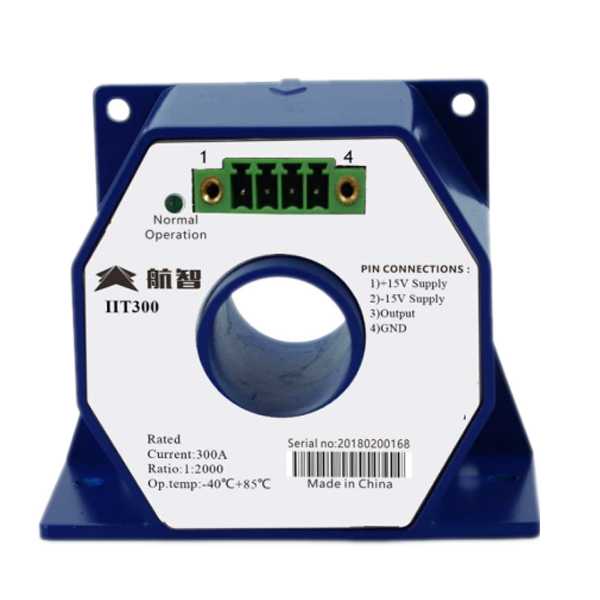
Types of Industrial Current Sensors
There are many types of current sensors used in industrial applications, including:
Current transformers
These sensors use induction and the natural magnetic field to measure current. They are commonly used in industrial environments.
Shunt resistors
These resistors have a precise, low resistance and are used to measure current by measuring the voltage drop across them.
Rogowski coils
These sensors use a flexible coil wrapped around a current-carrying conductor to measure alternating current. They are used for measuring high-speed current transients, pulsed currents, or 50/60 Hz line power.
These sensors are reliable and sensitive, and can measure a few milliamperes of direct current. They are often used for battery monitors.
These sensors produce a Hall voltage when the magnetic flux density around them is above a threshold. They are well-suited for current sensing applications.
These sensors can be clamped onto existing electrical wiring to measure the current passing through.
Current sensors are also known as current transducers or current sense transformers. They can be used in a variety of applications, such as controlling the electrical parameters of a locomotive engine or measuring the state of charge of an electric car battery.
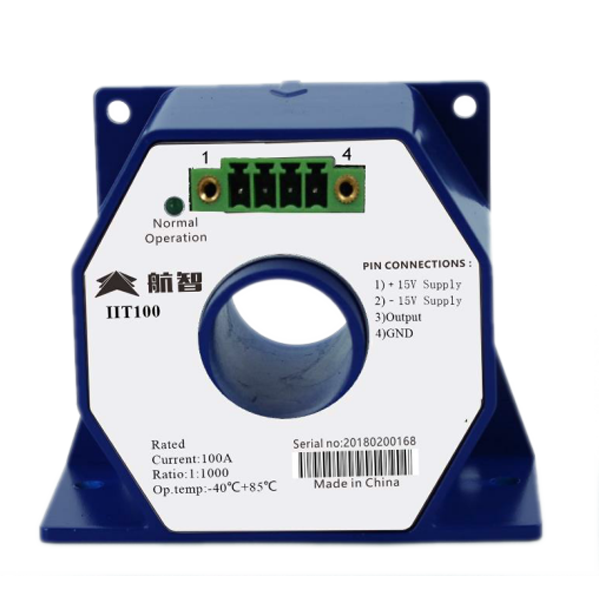
How Current Sensors Enhance Industrial Efficiency?
Current sensors contribute to the improvement of energy efficiency in industrial processes in several ways:
Real-Time Monitoring and Control:
Current sensors provide real-time data on the current flowing through electrical systems. This allows for immediate detection of anomalies and adjustments to be made promptly, ensuring optimal performance and preventing potential failures. By continuously monitoring current levels, these sensors can detect overloads and potential short circuits, thereby preventing damage to equipment and ensuring the safety of the system and personnel.
Energy Consumption Analysis:
Sensors can monitor energy consumption in manufacturing processes, analyzing energy usage patterns. This allows manufacturers to identify inefficient operations and make necessary adjustments to reduce energy consumption. This is particularly important in industries where energy costs are a significant part of the operational expenses.
Optimized Power Management:
In applications such as electric vehicles and industrial drives, current sensors are crucial for managing power efficiently. They help in balancing the load and ensuring that power is distributed optimally across different components. This leads to reduced energy waste and improved overall efficiency.
Predictive Maintenance:
Wireless current sensors enable remote monitoring of machine performance, allowing for predictive maintenance. By identifying potential issues before they lead to failures, these sensors help in reducing downtime and maintaining consistent energy efficiency.
Thermal Management:
By monitoring current, sensors can help in managing the thermal load on electrical systems, preventing overheating and extending the lifespan of components. This, in turn, reduces the need for frequent replacements and maintenance, leading to lower energy consumption and costs.
Integration with Industrial IoT:
Current sensors can be integrated with Industrial IoT solutions, providing data that can be analyzed to optimize processes further. This integration allows for smarter, more efficient industrial operations, reducing energy waste and improving overall efficiency.
Low-Power Operation:
Some current sensors, such as those using Hall effect technology, have low power consumption characteristics. This means they can effectively lower the overall energy consumption of the system, contributing to improved energy efficiency.
In summary, current sensors enhance energy efficiency in industrial processes by providing real-time data, analyzing energy consumption patterns, optimizing power management, enabling predictive maintenance, managing thermal loads, integrating with IoT, and operating with low power consumption.
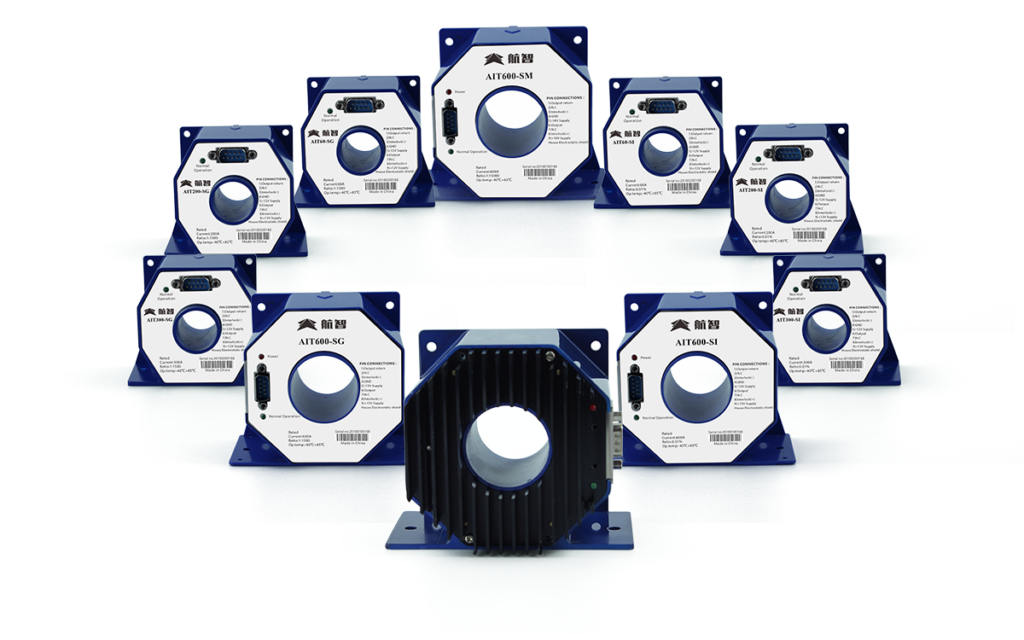
How Do I Choose a Current Sensor for Industrial Needs?
The following factors should be considered when selecting a current sensor suitable for industrial needs.
Understand Your Application Requirements
Before select a transducer, you should know what you need it for. such as the type of current (AC or DC), the range of current values you need to measure, and the required accuracy.
Consider Right Measurement Range
Current sensors have a certain range of current and can measure with high precision; This range is called its measurement range. It is crucial to choose sensors with a measurement range. If the range is too high, sensor overload is a risk, while if the range is too low, the entire current range cannot be measured. The resolution of the sensor or the minimum current change it can detect is also crucial.
Care About the Sensor’s Accuracy and Linearity
Accuracy and linearity are equally important considerations for transducer. The accuracy is how closely its readings match the real values, while its linearity of a sensor is its ability to retain a consistent sensitivity over its measurement range. To guarantee precise and trustworthy readings, a sensor with good accuracy and linearity should be used.
High-precision transducers should have low error rates and provide consistent, reliable readings. Hangzhi IIT industrial current sensor products have high accuracy, linearity & stability, and low temperature drift and zero drift features, and are providing services to our customers with the top performance and effective cost.
Consider Response Time
Response time refers to the time required for a sensor to record changes in current and generate appropriate output signals. Selecting a sensor with a quick reaction time guarantees precise and timely readings. If the reaction time is too long, the sensor or circuit might be damaged in situations where the current is constantly shifting.
Evaluate Output Signal Type
Check the type of signal that the current transducer sends out. Typical output types include digital signals and analog signals (current or voltage). Verify that the transducer’s output signal is compatible with your control system or data acquisition device.
Environmental Conditions, Mounting and Installation
Consider the operating environment, including temperature range, humidity, and potential exposure to chemicals or vibration, and choose a transducer that can withstand these conditions.
Ensure the transducer’s mounting and installation requirements align with your system’s capabilities and constraints. Isolation is also one of the factors in choosing sensors. Ensure the transducer provides adequate electrical isolation for safety and to prevent signal interference.
Check Compatibility with Existing Systems
Check the compatibility of the current transducer with your existing systems. Ensure the transducer’s physical size, mounting options, and electrical connections fit seamlessly with your setup.
Compatibility reduces the need for additional modifications and ensures smooth integration. Verify that the transducer meets the standards and specifications required for your system.
Compliance, Standards and Cost
Check that the transducer meets any relevant industry standards and regulations for your application. Consider the cost of the transducer in relation to your budget and the value it provides in terms of performance and reliability.
Check Manufacturer Reputation
Before you buy a current transducer, find out how well-known the company that made it is. Read reviews and ask for recommendations from industry professionals. Choose a transducer from a reputable manufacturer with good customer support and a reliable track record.
Boost Your Industrial Efficiency with Hangzhi Precision’s Current Sensors
Current sensors are indispensable tools in enhancing industrial efficiency. In the era of Industry 4.0, the role of current sensors is only set to grow, as they become more sophisticated and integrated into complex industrial systems. As technology advances, current sensors will continue to play a critical role in driving industrial efficiency and innovation.
Shenzhen Hangzhi Precision Electronics Co., Ltd. is a technology-leading enterprise dedicated to the research and development, production, sales and solution customization of high-precision current sensors, voltage sensors and high-precision electrical measuring instruments. We strive to build a well-known brand of precision current sensors and precision electrical measuring instruments in the DC field, and strive to develop into an internationally leading leader in precision electronics in the field of DC systems.